Qingdao Beisu Machinery Co., Ltd.
Hdpe Spiral Winding Pipe Production Line
Hdpe Spiral Winding Pipe Production Line
HDPE Hollow Wall Winding Pipe Extrusion Line
DN200-4500mm HDPE hollow wall winding pipe uses high-density polyethylene as the main raw material, adopts spirally winding forming technology, the inner and outer pipe walls are flat, ring stiffness classes from SN2 to SN16, frictional resistance is small,acid-resistant, alkali-resistant, anti-corrosion, non-toxic, compressive, not easy to age, and the service life is more than 50 years. The construction is convenient and the construction cost is low. In china, it has become a substitute for cement pipes, cast iron pipes, and glass pipes.
Extrusion line include:
1.Conical Twin screw extruder or High speed single screw Extruder,
2.Cladding Co-extrusion die,
3.Vacuum calibration water tank,
4.Cooling water tank,
5.Hauling machine,
6.Spiral forming unit,
7.Automatic Cutter,
8.Automatic Stacker.
Process Flow:
1. The raw materials are heated, melted, further mixed and plasticized in the extruder screw and barrel. The plasticized melt is pushed by a screw into the flow channel of the die head. 2. The die head also has a heating function. The heated melt flows through the flow channel inside the die head to form a tubular shape. The tubular hot melt from the die head enters the vacuum cooling tank. 3. Vacuum water tank produces vacuum, and cooling water is sprayed inside the tank. There is a calibration mold at the entrance of the vacuum water tank, and the hot melt will pass through the calibration mold. The vacuum will cause the melt to adsorb on the calibration die. The cooling water will cool the melt. At this stage a custom profile will be formed and will be moved to a cooling tank for further cooling. 4. The profiles are pulled out by the drawing machine, spiral winding by the auxiliary winding machine, and hot melt adhesive extruder extrudes hot melt adhesive, so that the profiles are attached to each other, and spiral winding forms a hollow wall winding tube. 5.: After the hollow wall winding tube is formed, move to the cutting machine. 6. The cutter can cut the pipe according to the required length. After cutting, the pipe will be moved to the stacker. Stacker has a roller to make the pipe spiral movement, with weighing and unloading device, reduce manual use.
Main technical parameter
Model
|
BSZKB- 800
|
BSZKB1200
|
BSZKB-1600
|
BSZKB-2400
|
BSZKB-3000
|
BSZKB-4000
|
Extruder
|
SJ-90/SJ-65
|
SJ-100/SJ-75
|
SJ-100/SJ-75
|
SJ-120/SJ-90
|
SJ-120/SJ-90
|
SJ-150/SJ-90
|
Capacity
|
300/120
|
450/180
|
450/180
|
600/300
|
600/300
|
800/400
|
Diameter
|
200-800 mm
|
300-1200 mm
|
800-1600 mm
|
1200-2400 mm
|
2000-3000 mm
|
2400-4000mm
|
Line speed
|
5-10 m/min
|
5-10 m/min
|
5-10 m/min
|
5-10 m/min
|
5-10 m/min
|
5-10 m/min
|
Power
|
180 kw
|
250 kw
|
300 kw
|
400 kw
|
500 kw
|
600 kw
|


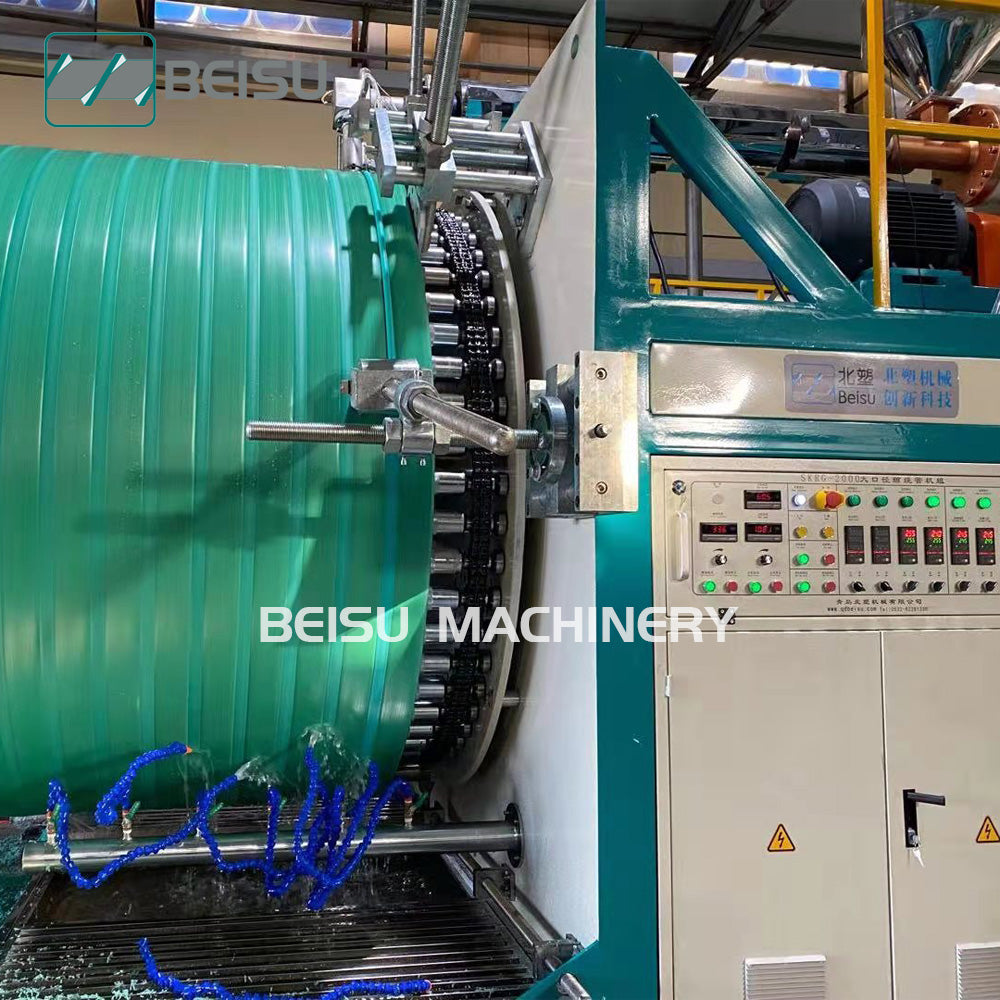
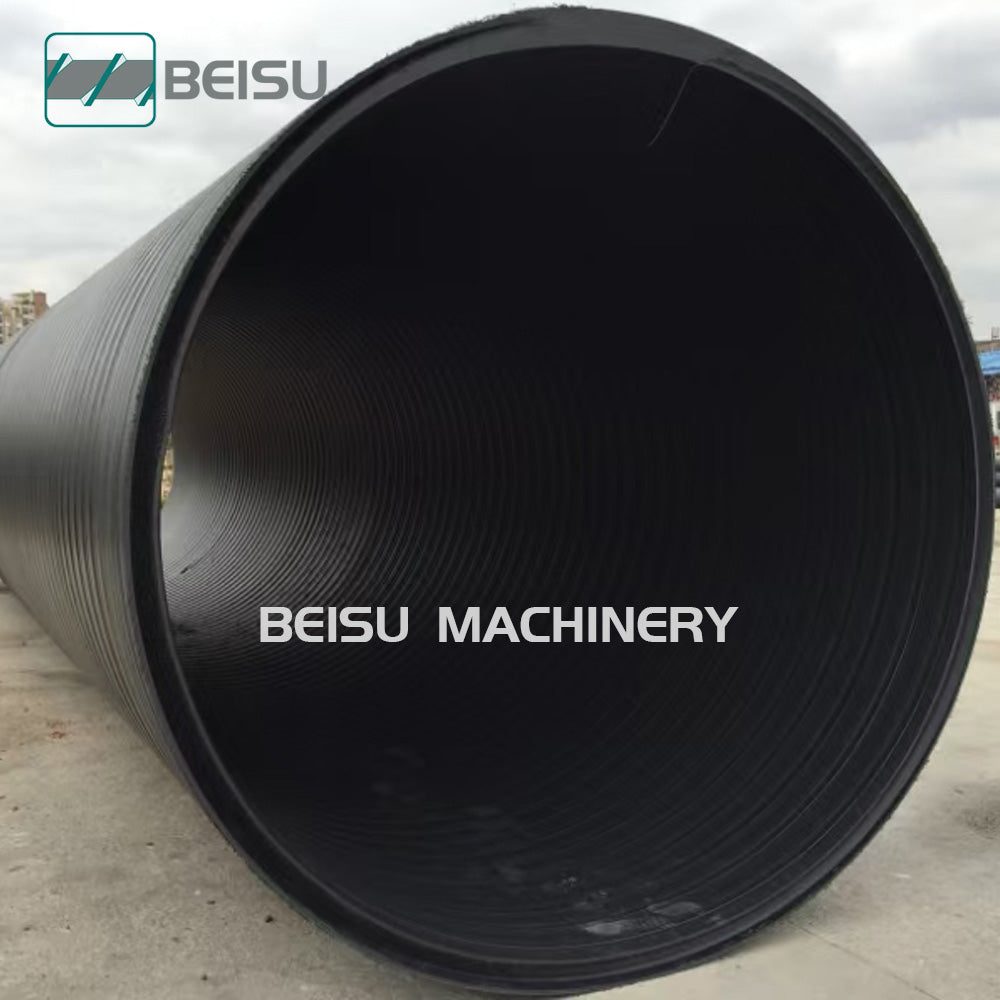
